In the modern construction industry, efficiency, durability, and energy conservation are more important than ever. Sandwich panels, a composite building material consisting of two outer skins and an insulating core, have become a game-changer. The production of these panels, using advanced sandwich panel production lines, has revolutionized construction by enabling faster, more efficient, and cost-effective building solutions.
In this article, we will explore how sandwich panel production lines are transforming the construction industry, the process behind their creation, and why they are essential for today’s building needs. We will also highlight the advantages of using sandwich panels in construction and how manufacturers are utilizing state-of-the-art production lines to meet the growing demand for these high-performance panels.
The Sandwich Panel Production Line
The sandwich panel production line is the machinery and technology responsible for creating these highly effective panels. It is an automated system that takes raw materials and processes them into finished sandwich panels ready for construction. The production line is designed to deliver high-quality panels in large volumes, ensuring that the panels meet the required standards for insulation, durability, and structural integrity.
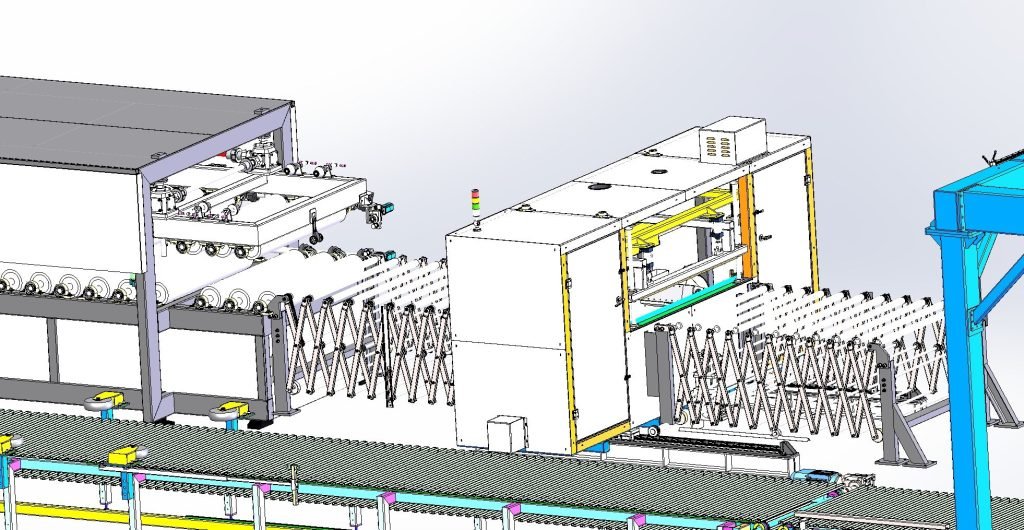
The Production Process
The sandwich panel production process involves several stages, each critical to ensuring the final product’s quality. Let’s take a look at the key stages of this process.
1. Raw Material Preparation
The production process begins with the preparation of the raw materials. The outer skins, which are typically metal coils (steel or aluminum), are unwound and prepped for bonding. The core material, whether EPS, PU, or mineral wool, is also prepared at this stage. The core material may come in pre-formed sheets or in liquid form, ready to be injected between the skins.
2. Surface Pre-Treatment
Before bonding, the outer skins are treated to ensure proper adhesion to the core material. This step may involve cleaning the surfaces to remove contaminants such as oils and dust. It is crucial that the bonding process is flawless to ensure the strength and durability of the final product. In some cases, a primer or adhesive may be applied to enhance the bond between the skins and the core material.
3. Lamination and Pressing
Once the skins are prepped, they are combined with the core material. This process is known as lamination. The core material is sandwiched between the two skins, and the entire assembly is passed through a pressing system. The press applies heat and pressure to bond the materials together, ensuring a strong, durable panel. For panels made with PU foam, the liquid foam is injected and expands between the skins, creating a solid core once it hardens.
4. Cutting and Shaping
After lamination, the continuous sandwich panel is cut to the desired length and shaped according to the required specifications. Automated cutting tools ensure precision, ensuring that each panel is of uniform size and quality. The cutting can be done in various shapes depending on the application, such as standard rectangular panels or panels with custom profiles for cladding and roofing.
5. Quality Control and Inspection
Quality control is a critical part of the production line. Each panel undergoes thorough inspection to ensure it meets the necessary standards. This includes testing for thermal insulation, mechanical strength, fire resistance, and visual inspection for defects. Panels that do not meet the quality standards are rejected.
Quality Check | Purpose | Testing Method |
---|---|---|
Thermal Insulation | Ensure panels provide effective insulation. | Conduct thermal conductivity tests. |
Strength | Ensure the panels are structurally sound. | Conduct mechanical strength tests. |
Fire Resistance | Verify the fireproof properties of the panels. | Perform fire exposure tests. |
Visual Inspection | Detect any defects in the panels. | Check for any cracks, dents, or surface imperfections. |
6. Packaging and Shipping
Once the panels pass quality control, they are packaged and prepared for shipment. Packaging ensures that the panels are protected from damage during transportation. Depending on the order size, the panels may be stacked and wrapped or placed on pallets to make handling easier. The packaging also helps prevent contamination or weather damage during transit.
How Sandwich Panel Production Lines Are Revolutionizing Construction
Sandwich panel production lines have brought several innovations that are changing the way buildings are constructed. These include the following:
1. Enhanced Efficiency and Speed
One of the main advantages of sandwich panel production lines is their speed and efficiency. Automated systems allow manufacturers to produce large quantities of panels in a short amount of time, significantly reducing lead times. This is crucial in the construction industry, where timely delivery of materials is essential to keep projects on schedule.
Additionally, these lines ensure that the production process is highly efficient, reducing the need for manual labor and minimizing errors that could arise from human involvement.
2. Improved Insulation and Energy Efficiency
With growing concerns about energy consumption and the need for sustainable buildings, sandwich panels have become a vital component in energy-efficient construction. The core materials used in these panels—such as EPS, PU, and mineral wool—offer excellent thermal insulation, helping to reduce heating and cooling costs for buildings.
Panels with high insulation properties help maintain a comfortable indoor climate while minimizing the use of energy, contributing to both environmental sustainability and cost savings for building owners.
3. Superior Durability and Strength
Sandwich panels are known for their strength and durability. The bonding process in the production line ensures that the panels have the necessary structural integrity to withstand harsh weather conditions, including strong winds, snow, and heavy rain. Furthermore, the metal outer skins are resistant to corrosion, ensuring a long lifespan for the panels. These features make sandwich panels ideal for use in demanding environments such as industrial buildings, warehouses, and cold storage facilities.
4. Fire Resistance
Fire safety is a primary concern in building construction, and sandwich panels meet stringent fire resistance standards. Mineral wool and rock wool-based sandwich panels are particularly effective in preventing the spread of flames, making them an ideal choice for buildings where fire protection is critical, such as high-rise buildings and industrial facilities.
5. Cost-Effectiveness
By streamlining the manufacturing process, sandwich panel production lines help reduce production costs. The automation of tasks, combined with minimal waste and quick assembly times, lowers the overall cost of the panels. This, in turn, makes sandwich panels an affordable solution for large-scale construction projects. Builders can save money on labor, installation, and materials, making sandwich panels a cost-effective choice for many construction applications.
Applications of Sandwich Panels in Construction
Sandwich panels are widely used in various construction sectors, including:
- Residential and Commercial Buildings: Sandwich panels are used for walls, roofs, and floors, providing insulation and protection against the elements.
- Industrial and Agricultural Buildings: Due to their durability and insulation properties, sandwich panels are ideal for warehouses, factories, and agricultural buildings.
- Cold Storage and Refrigeration: With excellent thermal insulation properties, sandwich panels are commonly used in refrigerated storage facilities and cold rooms.
- Soundproofing: Panels made from mineral wool and other sound-absorbing materials are used in environments that require acoustic insulation, such as auditoriums, offices, and theaters.
Conclusion
Sandwich panel production lines are revolutionizing the construction industry by providing efficient, durable, and energy-efficient solutions for a wide range of applications. The use of automated machinery ensures high production rates, consistent quality, and minimal waste, making sandwich panels an ideal choice for modern building projects. As the demand for energy-efficient and sustainable buildings continues to grow, sandwich panels will remain at the forefront of construction innovation.