sandwich panel production line
Clean Room Box Sandwich Panel automatic continuous production line
Application Fields
- Clean room box sandwich panel , also known as purification box panel, is a composite panel made of color-coated steel, stainless steel, aluminum alloy board and other materials as the surface material.
- Purification box panel has unique dust-proof, anti-static, antibacterial and other effects. It is widely used in electronics, pharmaceuticals, food, biology, aerospace, precision instrument manufacturing and scientific research and other clean engineering fields with strict requirements on indoor environment.
Production process
- Uncoiling
- Panel box roll forming machine
- Panel translation
- Core material feeding machine
- Core material glue coating
- core material into frame
- sandwich panel composite (hot press crawler machine)
- Stacking
- winding and packing
Plate composition
Composition:
- Upper panel + core material + lower panel + keel
(the frame formed by splicing around is also called “keel”)
Core material options:
- Rock wool
- Single-sided glass magnesium rock wool
- Double-sided glass magnesium rock wool
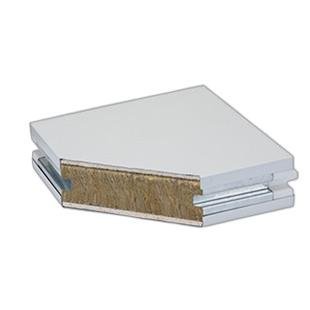
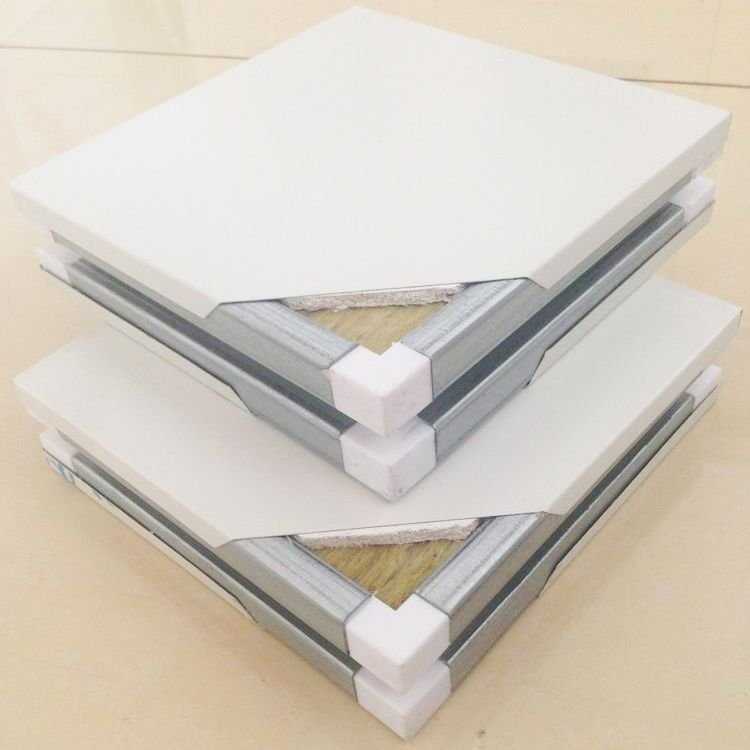
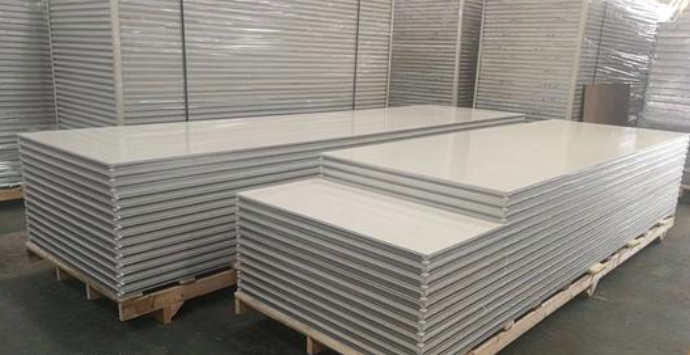
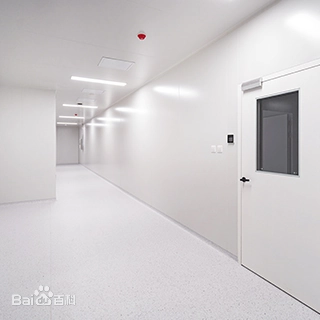
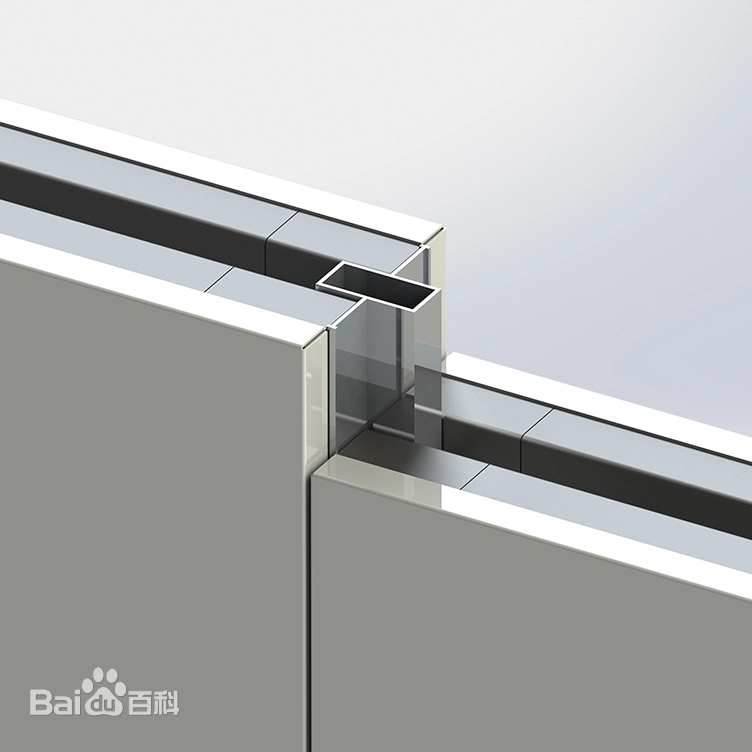
Production line components
Uncoiler and panel box roll forming machine
- The hydraulic uncoiler is used for automatic uncoiling and is equipped with a hydraulic lifting platform for quick coil replacement.
- The panel box roll forming machine is used to press the panel into a box shape, similar to the panel pressing of the roof panel.

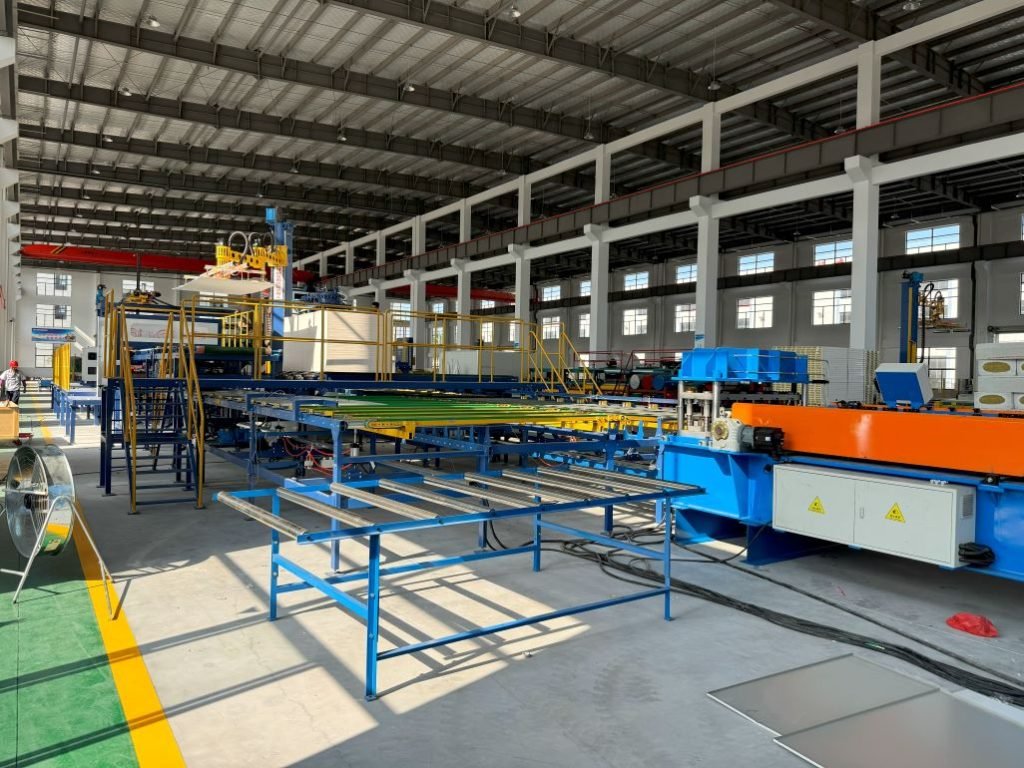
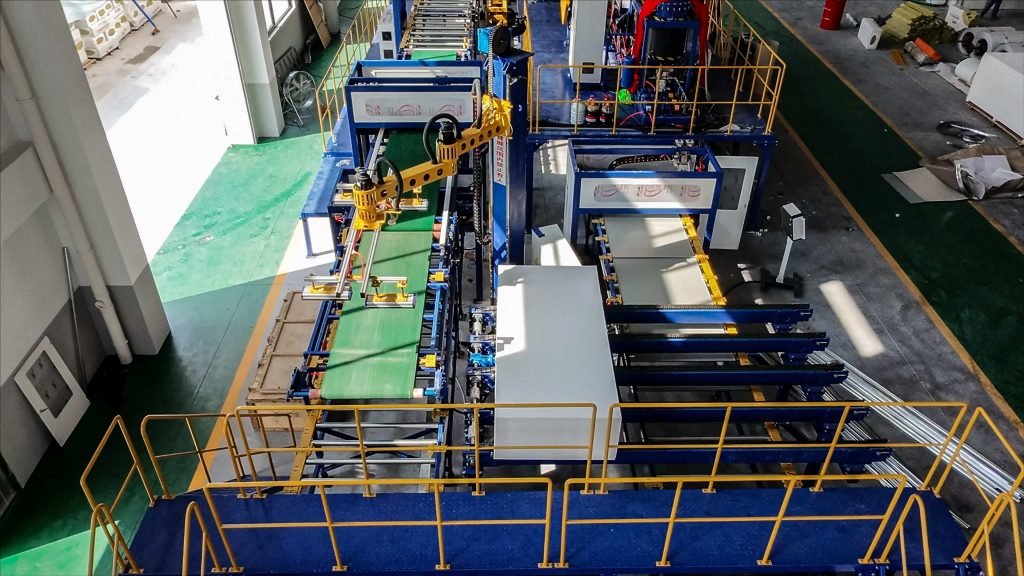
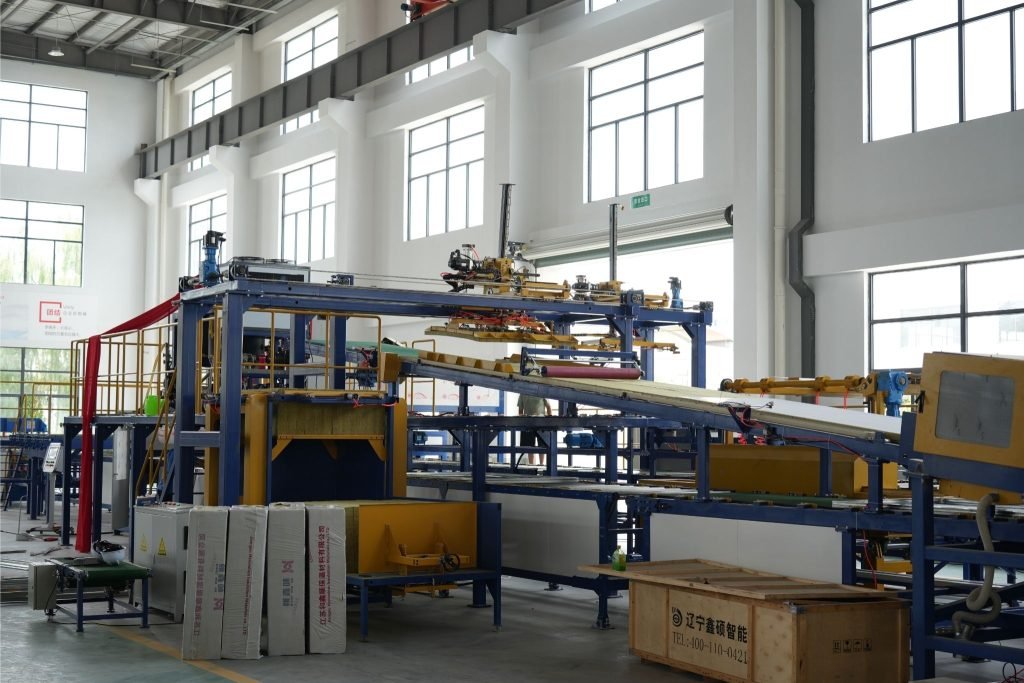
Core material feeding machine
As this production line produces with different core materials, we uses a truss rock wool feeder and a four-axis multi-functional feeder to meet the complex loading needs of various core materials.
Glue spraying machine
The entire fully automatic production line has three glue spraying machines.
Upper panel box glue spraying.
Lower panel box glue spraying.
Xinshuo’s self-developed glue spraying system can change the glue spraying speed and mixing ratio with one click on the computer. It is automated and intelligent.
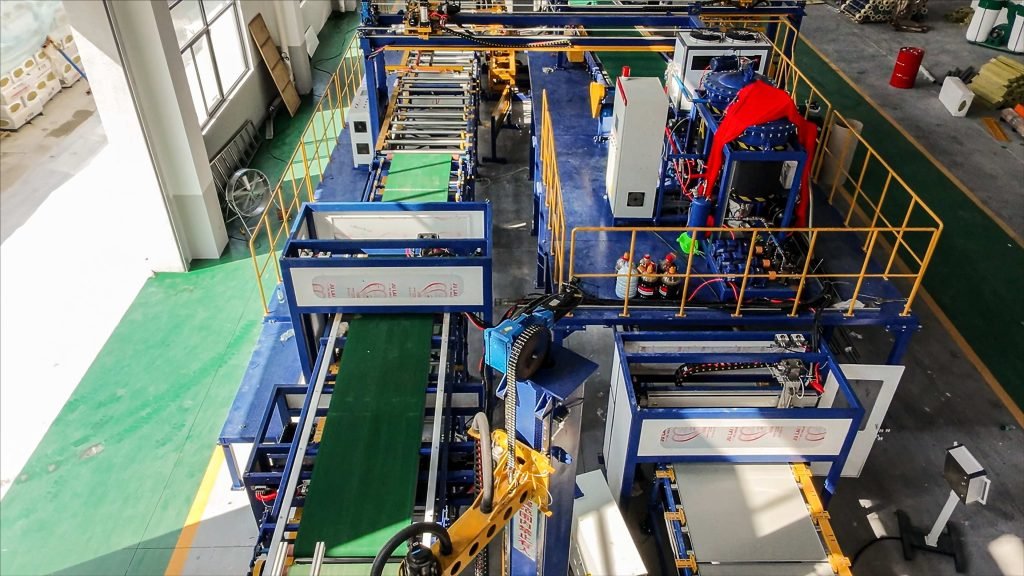
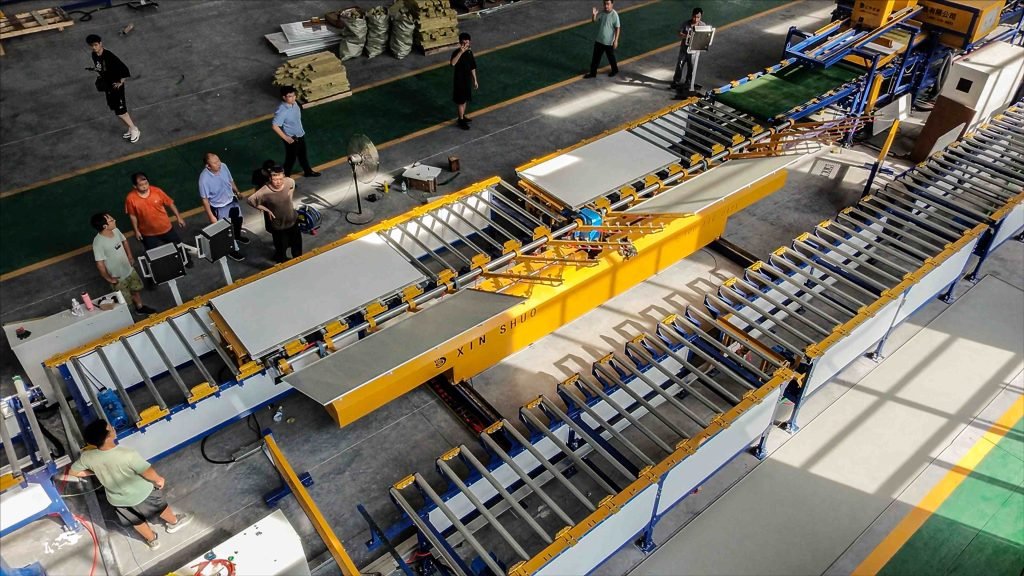
panel Servo-tracking compounding system
In the production process of clean room sandwich panel, the glue-coated upper panel is buckled onto the core material.
Our production line adopts tracking lamination method to ensure that the core material can be laminated while the panels are continuously transported.
The entire production line uses servo motors and PLC communication panels to track the buckling error, which is almost zero. The accuracy is very high.
double belt conveyor crawler system
After the panels are laminated, the glue needs to be cured. We use a double belt conveyor crawler system, which has the advantage of continuous production.
The double belt conveyor crawler system has heating and flattening conveying functions. This conveying method can make the panels tightly laminated during continuous production.
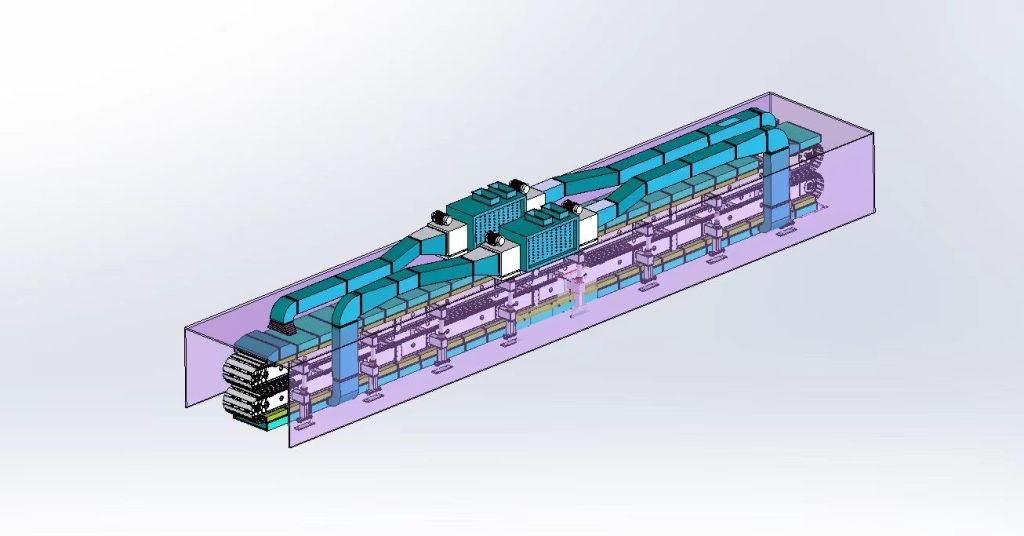
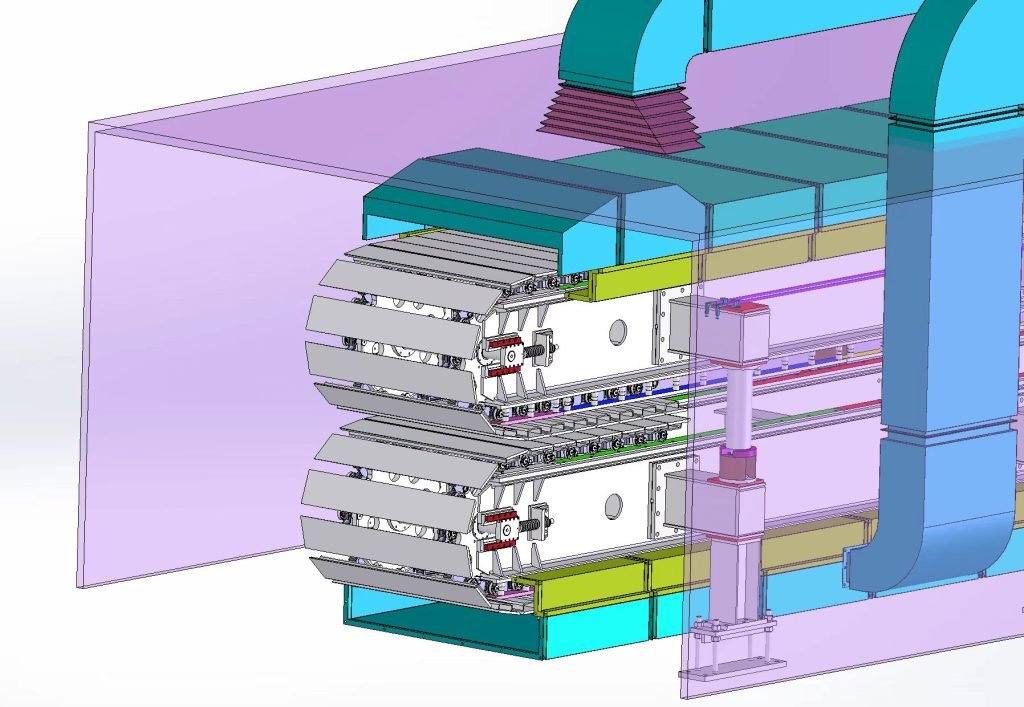
stacking machine
- Our palletizers come in various forms, and you can choose a palletizer with different functions based on actual conditions.
winding and packing
- Packaging machine is a kind of supporting equipment for production line.
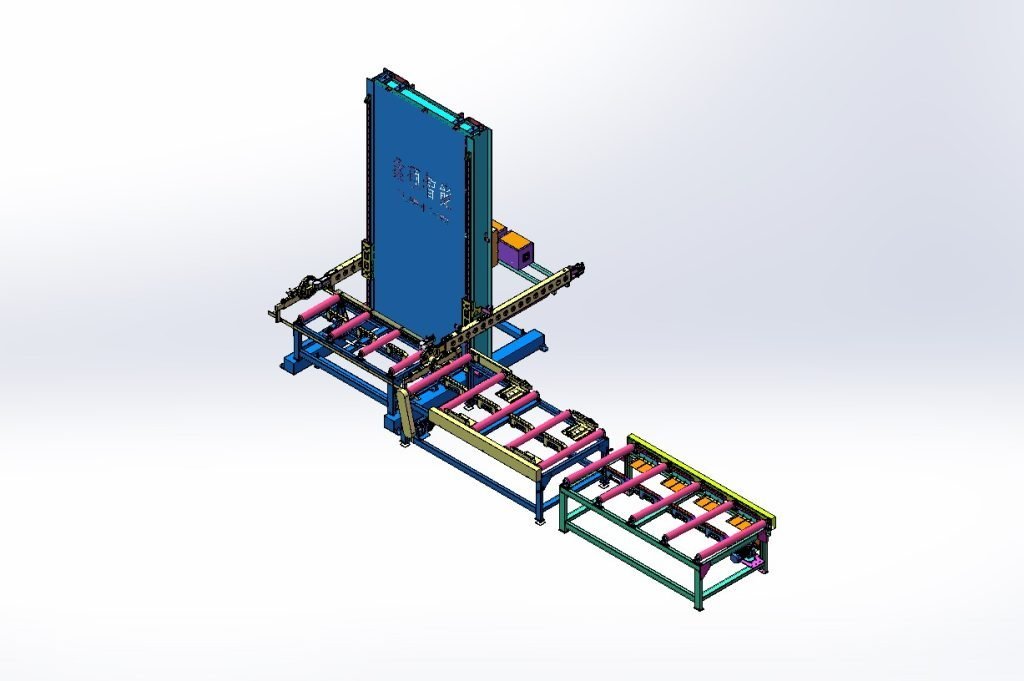
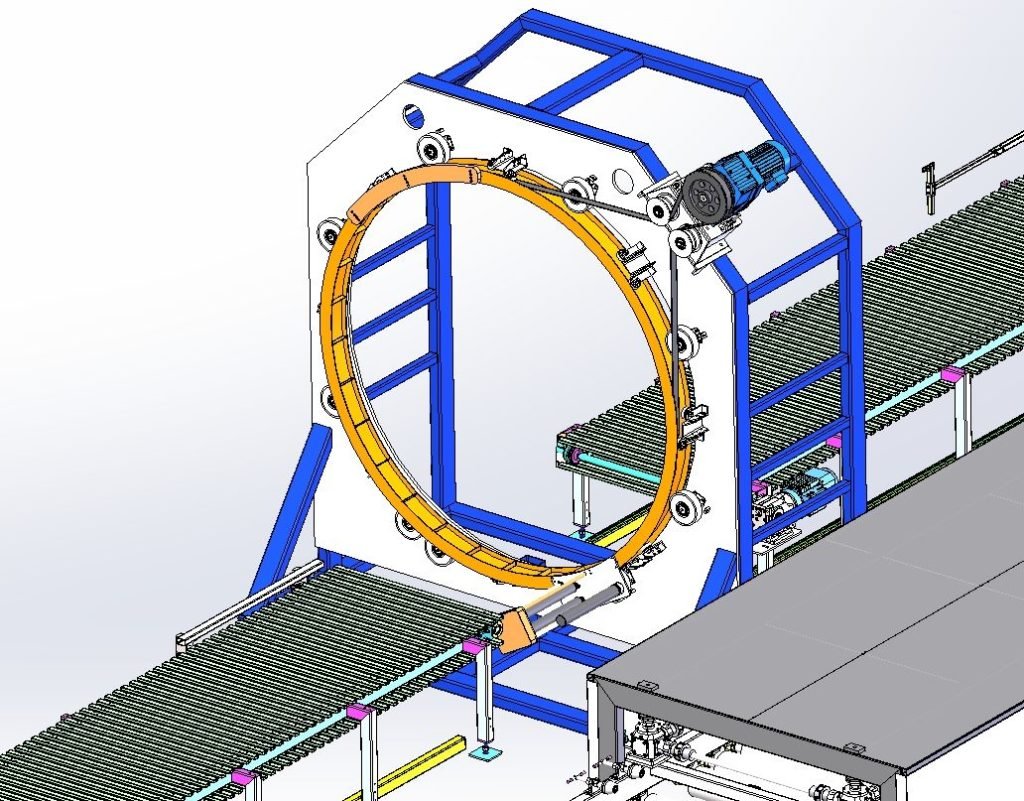
Production line parameters
Total length of production line: 112 meters (not absolute)
Line width: 9.8 meters (not absolute)
Production speed: 4-6m/min
Sheet production length: 2000-10000mm (customizable)
Sheet thickness: For example: 50/75/100/ (customizable)
Sheet width: depends on the panel width of the box forming machine and the core filling.
- We have independent processing and production capabilities and a professional engineering design team! This gives us a high degree of freedom in customization!
- After years of independent research and development, we have improved the production process and maintained the original quality to upgrade the production efficiency, rise the production efficiency of clean panels.
- The original production line requires about 20 production employees, and the production efficiency is 1.5m/min.
- If use our production line, the demand for production employees is reduced by half, and the production efficiency is improved to 5m/min.
Get more information by following our social media !
LMS (production line management system )
- Xinshuo independently developed a fully automatic management system named Line Management System (LMS) Suitable for fully automated production lines.
- Fully automatic production line install with LMS will improve production efficiency and comprehensively reduce production and management costs. To achieve transform the factory to modernization and intelligence.
2.png)