Sandwich panels are composite building materials widely used in construction for their excellent insulation and structural properties. They consist of two outer layers, typically metal, and a core material that provides thermal and acoustic insulation. The production of these panels is facilitated by advanced manufacturing systems known as sandwich panel production lines, which integrate mechanics, chemistry, electrical control, and automation. This survey note provides a detailed examination of the production process, types of lines, automation, and future trends, based on extensive research.
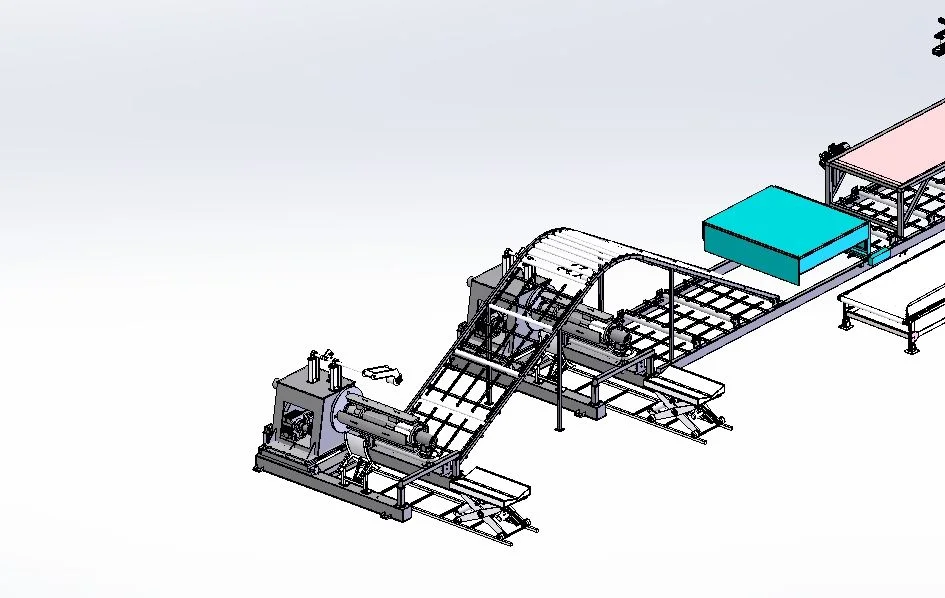
Definition and Components
A sandwich panel is defined as a building product with two metal faces and a rigid thermally insulating core, firmly bonded to act composively under load. The core can vary, including polyurethane (PU), polyisocyanurate (PIR), mineral wool, or expanded polystyrene (EPS), each offering different properties like fire resistance, insulation, and soundproofing. The outer layers, or facings, are usually steel or aluminum, providing durability and weather resistance.
Benefits in Construction
Sandwich panels are valued for their high strength-to-weight ratio, making them lightweight yet capable of bearing shear loads. They offer excellent thermal and acoustic insulation, reducing energy consumption in buildings. Their prefabricated nature allows for quick installation, reducing construction time and costs, and they are versatile for applications in walls, roofs, and cold storage.
Production Process Overview
The production process is typically continuous, involving several key stages:
- Uncoiling and Roll Forming: Metal coils are unwound and shaped into the desired profile using roll forming units. This step ensures the metal sheets are ready for lamination, with hydraulic uncoilers providing stable feeding.
- Core Material Preparation: The core material is prepared based on type. For PU/PIR, a foaming system mixes and applies the foam; for mineral wool, boards are cut and fed into the line. This step varies by insulation needs, with PU offering low thermal conductivity and mineral wool providing fire resistance.
- Gluing and Bonding: Adhesive is applied to ensure bonding between the core and metal sheets. For PU, the foam itself acts as a binder, while mineral wool lines use glue systems for adhesion.
- Lamination: The metal sheets and core are pressed together in a laminating unit, ensuring uniform thickness and alignment. This step may involve high pressure and heat for PU to cure properly.
- Cutting: The continuous panel is cut to desired lengths using automated cutting units, such as band saws for PU or specialized cutters for mineral wool, ensuring precision.
- Cooling and Curing: For PU panels, a cooling conveyor allows the foam to set, ensuring structural integrity. Mineral wool panels may not require this step, depending on the adhesive used.
- Stacking and Packing: Finished panels are automatically stacked and packed, often with plastic wrap, using systems like vacuum suction plates for efficiency.
Types of Production Lines
Production lines are categorized by core material, each with specific equipment:
- PU/PIR Lines: These lines use foaming systems to apply PU or PIR, known for low heat conductivity and high insulation. They include PU metering machines for precise foam application and double belt conveyors for curing. A typical line can produce panels at 14 meters per minute for medium thicknesses (40-50 mm), yielding about 1,180,000 meters annually with 80% efficiency.
- Mineral Wool Lines: These lines handle mineral wool boards, offering fire resistance and soundproofing. They include mineral wool supplying systems and glue applicators, with production speeds varying by thickness. The process involves board cutting and alignment, with automation ensuring continuous production.
The choice between continuous and discontinuous processes depends on production volume, with continuous lines preferred for high output and discontinuous for specialized shapes.
Automation and Efficiency
Automation is integral to modern sandwich panel production lines, enhancing efficiency and quality. Lines are fully automated, controlled by PLCs and HMIs, with sensors monitoring each stage. Key automated components include:
- Uncoiler and Roll Forming: Hydraulic systems ensure stable coil feeding and shaping, with 2+2 systems allowing continuous operation without stopping.
- Core Material Handling: Automated systems feed and process core materials, with PU lines using servo motors for foam application and mineral wool lines automating board cutting.
- Lamination and Pressing: Automated laminating units ensure uniform bonding, with double belt conveyors synchronizing movement for curing.
- Cutting and Finishing: Automated cutting units, like band saws, ensure precise lengths, followed by automated stacking and packing, reducing labor and error.
This automation minimizes human intervention, increases production speeds, and ensures consistency, with lines capable of handling various materials like PVC and SIPs for diverse applications.
Quality Control Measures
Quality control is critical, involving raw material inspection, in-process checks, and final product testing. Automated monitoring systems detect defects, ensuring panels meet standards for insulation, fire resistance, and structural integrity. Calibration of production lines and workforce training further enhance quality.
Environmental Considerations
Environmental impact is increasingly important, with trends towards sustainable materials. Bio-based insulation cores and recyclable facings are emerging, aligning with green building practices. The use of pentane as a blowing agent in PU lines, for example, reduces environmental footprint.
Future Trends
The sandwich panel market is projected to grow at a CAGR of 5.2% from 2024 to 2032, reaching USD 22.03 billion, driven by demand for energy-efficient and sustainable construction. Key trends include:
- Sustainability: Innovations in eco-friendly cores, like bio-based materials, and recyclable facings, supported by stringent regulations on energy efficiency.
- Material Innovation: Development of new core materials with enhanced properties, such as improved fire resistance and insulation, and advanced facings for corrosion resistance.
- Automation and Efficiency: Continued advancements in production line automation, reducing waste and increasing productivity, with AI and IoT integration for real-time monitoring.
- Customization: Growing demand for customized panel designs to meet specific architectural and functional needs, driven by urbanization and infrastructure growth in developing economies.
Comparative Analysis of Production Lines
To illustrate the differences, consider the following table comparing PU and mineral wool lines:
Aspect | PU/PIR Line | Mineral Wool Line |
---|---|---|
Core Material | Foam (PU/PIR), applied via foaming system | Boards (mineral wool), fed and cut |
Key Equipment | PU metering machine, foaming portal, double belt conveyor | Mineral wool supplying system, glue applicator |
Production Speed | Up to 14 meters/minute for 40-50 mm thickness, high output | Varies, typically lower for specialized shapes |
Insulation Properties | Low thermal conductivity, high insulation, good for cold storage | Fire resistance, soundproofing, suitable for fireproof buildings |
Environmental Impact | Uses pentane blowing agent, moving towards bio-based cores | Generally more sustainable, recyclable cores |
Automation Level | High, with servo motors for foam application, automated stacking | High, with automated board cutting and lamination |
This table highlights the tailored approaches for different core materials, influencing production efficiency and application.
Conclusion
Sandwich panel production lines are critical for manufacturing efficient, high-quality construction materials. The process, varying by core material, is highly automated, ensuring consistency and scalability. Future trends towards sustainability and innovation will further enhance their role in green construction, meeting global demands for energy-efficient buildings.