Sandwich panels are multilayered construction materials consisting of two outer layers and an inner insulating core. They are widely used in construction due to their unique properties and versatility. The primary purpose of sandwich panels is to create durable and energy-efficient structures for residential, commercial, and industrial buildings.
The production process of sandwich panels begins with the selection of high-quality raw materials. The outer layers are typically made of metals such as steel or aluminum, while the inner core consists of insulating materials like polyurethane foam or mineral wool. These materials undergo several processing stages, including cutting, forming, and bonding, ensuring the strength and durability of the final product.
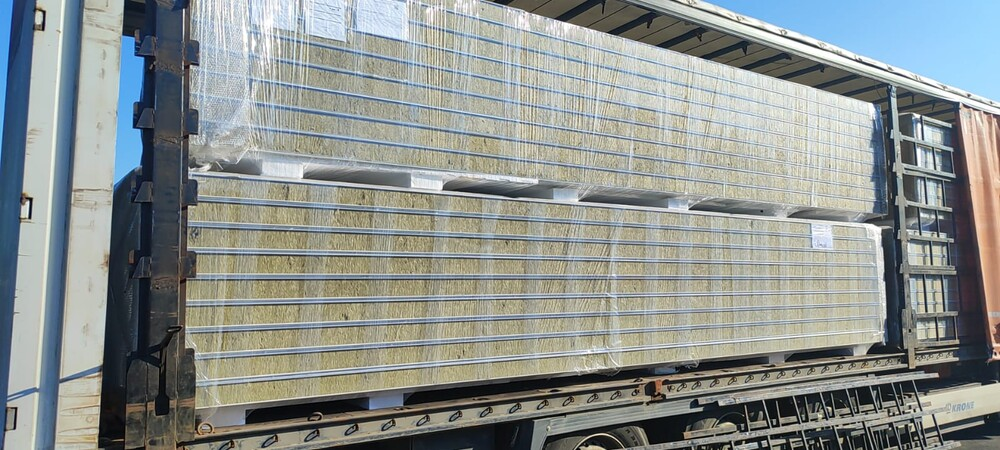
The use of sandwich panels offers numerous advantages:
- High thermal insulation, significantly reducing heating and cooling costs.
- Strength and resistance to external factors such as moisture, wind, and mechanical stress.
- Lightweight and easy installation, reducing construction time and costs.
- Environmental friendliness and safety, as many modern panels are made from eco-friendly materials.
Thus, the technology for producing sandwich panels, from raw materials to the finished product, enables the creation of reliable and efficient construction materials widely used in various construction sectors.
Raw Materials for Production
The production of sandwich panels begins with the selection and use of high-quality raw materials. This section examines the main types of materials used, such as metals and insulators, and discusses the quality standards that raw materials must meet.
One of the key components of sandwich panels is metal. The outer and inner layers are most commonly made from galvanized steel. These materials provide strength and durability to the finished product while protecting it from corrosion and mechanical damage. Galvanized steel, with its zinc coating, offers high resistance to atmospheric conditions, making it an ideal choice for construction applications.
Equally important is the insulating core. Commonly used insulators include mineral wool or polyurethane foam. Mineral wool, due to its non-combustible nature and excellent sound insulation, is suitable for facilities with stringent fire safety requirements. Polyurethane foam, with its high density and low thermal conductivity, ensures maximum energy efficiency.
The quality and standards of raw materials play a critical role in sandwich panel production. All materials must comply with international and national standards, such as GOST or ISO. This ensures that the products are safe, durable, and meet specified performance characteristics. Manufacturers rigorously monitor the quality of raw materials at all production stages, from their arrival at the factory to the finished product. Each component undergoes strict testing to ensure compliance with technical and environmental standards.
In summary, the production technology of sandwich panels involves the use of high-quality metals and insulators while adhering to stringent raw material quality standards. This results in reliable and efficient construction materials that meet modern requirements and ensure comfort and safety in use.
Stages of Sandwich Panel Production
The production of sandwich panels is a complex, multi-stage process that requires precise adherence to technology and quality control at every step. This section outlines the main stages of sandwich panel production, from material preparation to final processing and quality control.
Material Preparation and Processing
The first stage of sandwich panel production involves preparing and processing raw materials. The primary components are the facing materials and the insulator. Facing materials are typically made of metal, while the insulator is usually mineral wool or polyurethane foam. At this stage, materials undergo thorough quality checks to ensure compliance with standards, followed by cutting and processing for further use.
Layer Assembly and Bonding
The second stage involves assembling and bonding the layers of the sandwich panel. This process includes several steps:
- Application of adhesive to the facing materials.
- Placement of the insulator between the facing layers.
- Pressing the panels to ensure strong bonding of the layers.
These steps are performed synchronously in an automated, continuous production line. The use of high-quality adhesive and precise pressing technology guarantees the durability and reliability of the finished panels.
Final Processing and Quality Control
The final stage involves processing and quality control. Finished sandwich panels are tested for compliance with technical specifications, such as strength, thermal insulation properties, and resistance to external factors. Quality control is conducted at every production stage to ensure the high quality and reliability of the final product.