At Xinshuo Intelligent Production Line, we pride ourselves on delivering cutting-edge automation solutions that transform factories into modern, efficient, and intelligent production hubs. One of our flagship products, the Sandwich Panel Automatic Stacker, exemplifies this commitment. Designed as an integral part of our fully automated sandwich panel production line, this advanced system streamlines the stacking process, ensuring precision, speed, and reliability for manufacturers worldwide. In this comprehensive guide, we explore the technical specifications, operational features, and transformative benefits of the Sandwich Panel Automatic Stacker, showcasing why it is a must-have for sandwich panel production in industries ranging from construction to clean room engineering.
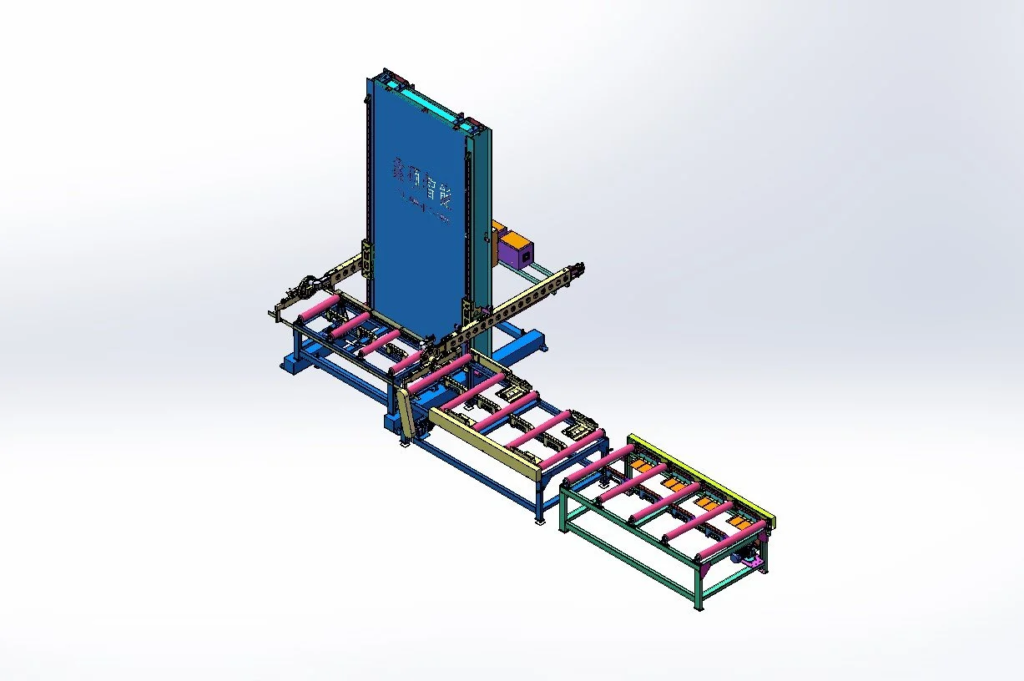
With over a decade of expertise in mechanical automation, Xinshuo has engineered the Automatic Stacker to meet the evolving demands of the global market. Whether you produce rock wool sandwich panels, polystyrene (EPS) panels, glass magnesium panels, or magnesium oxide sulfide panels, this system enhances productivity while maintaining the highest standards of quality. Let’s dive into the details of this innovative product and discover how it can elevate your manufacturing operations.
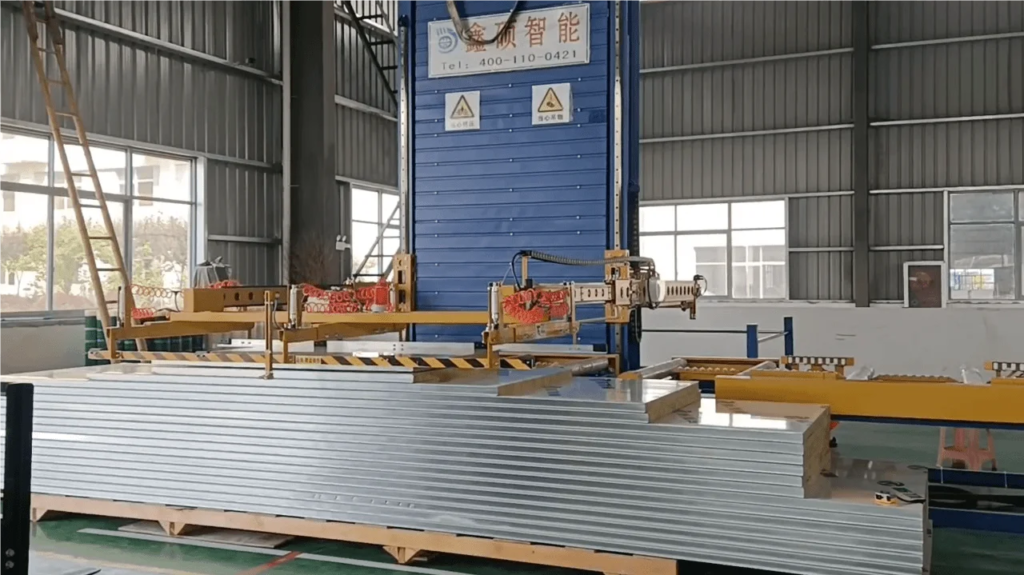
1. Introduction to the Sandwich Panel Automatic Stacker
Sandwich panels are versatile composite materials widely used in construction, clean room engineering, and industrial applications due to their lightweight structure, excellent insulation properties, and durability. These panels typically consist of two outer layers—often steel or aluminum—sandwiching an insulating core made from materials like rock wool, EPS, glass magnesium, or magnesium oxide sulfide. The production process involves multiple stages, including forming, cutting, and stacking, with the latter being a critical step to ensure panels are organized for storage, transportation, or installation.
The Sandwich Panel Automatic Stacker is the cornerstone of Xinshuo’s fully automated production line, designed to handle this final stage with unmatched efficiency. By automating the stacking process, it eliminates manual labor, reduces the risk of panel damage, and ensures consistent output, making it an indispensable tool for manufacturers aiming to scale operations and improve quality control. As the global sandwich panel market continues to grow—projected to reach a CAGR of 6.7% from 2023 to 2030 (Grand View Research)—the demand for automation solutions like Xinshuo’s stacker is at an all-time high.
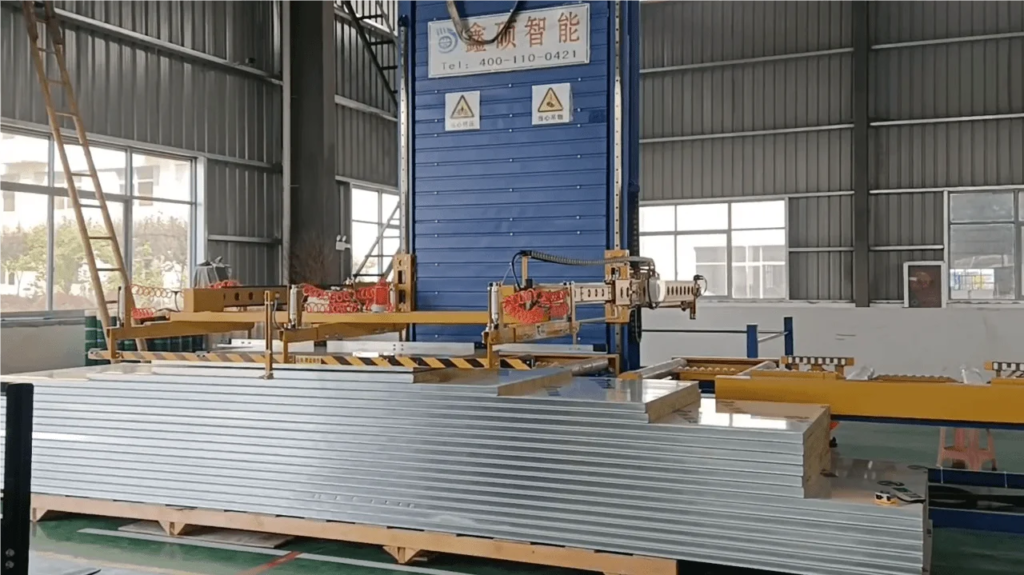
2. Technical Specifications of the Sandwich Panel Automatic Stacker
The Sandwich Panel Automatic Stacker is engineered to accommodate a wide range of panel types and sizes, reflecting Xinshuo’s commitment to versatility and precision. Below, we outline its key technical parameters, which highlight its capability to meet diverse manufacturing needs.
2.1 Panel Dimensions
- Panel Length: Adjustable from 2,000 mm to 12,000 mm
- Panel Width: 600 mm to 1,200 mm
- Panel Thickness: 50 mm to 200 mm
These specifications allow the stacker to handle standard panel sizes used in construction, as well as custom dimensions for specialized applications like clean room panels. The adjustable settings ensure flexibility, enabling manufacturers to adapt to various project requirements without additional equipment.
2.2 Stacking Capacity
- Maximum Stacking Height: 1,200 mm (approximately 24 panels at 50 mm thickness)
- Maximum Load Capacity: 2,000 kg per stack
With a robust design, the stacker can manage high-volume production runs, supporting up to 2,000 kg per stack. This capacity ensures it meets the needs of large-scale manufacturers while maintaining stability and safety during operation.
2.3 Speed and Efficiency
- Stacking Speed: Up to 10 panels per minute (varies by panel size and thickness)
- Cycle Time: Average of 6 seconds per panel
The stacker’s high-speed performance ensures it keeps pace with upstream production processes, preventing bottlenecks and maximizing throughput. This efficiency is a game-changer for manufacturers aiming to meet tight deadlines and large orders.
2.4 Automation and Control
- Control System: PLC-based with touchscreen interface
- Sensors: Photoelectric sensors for precise panel detection and alignment
- Motors: Servo motors for accurate positioning
Powered by a state-of-the-art PLC system, the stacker offers real-time control and monitoring. The intuitive touchscreen interface allows operators to adjust parameters—such as stacking speed or panel size—effortlessly, while servo motors and sensors ensure pinpoint accuracy in every stack.
2.5 Power and Energy Consumption
- Power Supply: 380V, 50Hz, 3-phase
- Power Consumption: 5 kW (average during operation)
Designed with energy efficiency in mind, the stacker consumes just 5 kW on average, reducing operational costs and supporting sustainable manufacturing practices—an increasingly important factor in today’s eco-conscious market.
2.6 Safety Features
- Emergency Stop: Immediate system halt for safety
- Protective Barriers: Enclosed design to shield moving parts
- Load Sensors: Prevent overloading and ensure safe stacking
Safety is paramount at Xinshuo. The stacker includes multiple safety features to protect operators and equipment, ensuring compliance with international standards and providing peace of mind in high-paced production environments.
3. Operational Features of the Sandwich Panel Automatic Stacker
The Sandwich Panel Automatic Stacker is more than just its technical specs—it’s a system designed for usability, flexibility, and seamless integration. Below are its standout operational features that set it apart in the industry.
3.1 Fully Automated Operation
The stacker operates autonomously, detecting, aligning, and stacking panels with minimal human intervention. This reduces labor costs and eliminates errors associated with manual handling, allowing operators to focus on oversight and maintenance.
3.2 Adjustable Stacking Patterns
- Flat Stacking: Ideal for standard wall and roof panels
- Interlocked Stacking: For panels with unique edge profiles
- Offset Stacking: Accommodates panels with protruding features
This adaptability ensures the stacker can handle diverse panel designs, from roofing to clean room applications, without requiring extensive reconfiguration.
3.3 Seamless Integration
Designed to complement Xinshuo’s sandwich panel production line, the stacker integrates effortlessly with upstream processes. It can also be retrofitted into existing lines, offering a cost-effective upgrade for manufacturers seeking automation.
3.4 Real-Time Monitoring
With advanced sensors and PLC controls, the stacker provides real-time data on stacking speed, alignment, and load status. Diagnostic tools alert operators to potential issues, minimizing downtime and ensuring consistent performance.
3.5 Material Compatibility
Compatible with rock wool, EPS, glass magnesium, and magnesium oxide sulfide cores, the stacker supports all panel types produced by Xinshuo’s line, offering unparalleled versatility for manufacturers.
4. Benefits of the Sandwich Panel Automatic Stacker
The stacker delivers tangible advantages that enhance productivity, reduce costs, and improve quality. Here’s how it transforms manufacturing operations:
4.1 Enhanced Productivity
With a stacking speed of up to 10 panels per minute, the stacker boosts throughput, enabling manufacturers to meet growing demand efficiently.
4.2 Cost Savings
By automating stacking, it reduces labor needs by up to 50%, freeing resources for other critical tasks and lowering operational expenses.
4.3 Superior Quality
Precise alignment and gentle handling minimize panel damage, ensuring consistent quality that meets customer expectations.
4.4 Safety Improvements
Eliminating manual handling reduces workplace injuries, creating a safer environment for your team.
4.5 Sustainability
Low energy consumption aligns with green manufacturing goals, helping you reduce your environmental footprint.
5. Applications Across Industries
- Construction: Wall and roof panels for buildings
- Clean Rooms: Purification panels for electronics and pharmaceuticals
- Cold Storage: Insulated panels for refrigeration
- Prefabricated Housing: Panels for modular homes
Its versatility makes it an ideal solution for diverse manufacturing needs.
6. Integration with Xinshuo’s LMS
The stacker pairs seamlessly with Xinshuo’s Line Management System (LMS), a fully automatic management tool that optimizes production. LMS provides real-time analytics, enhancing efficiency and transforming factories into intelligent operations.
7. Xinshuo’s
The Sandwich Panel Automatic Stacker is a testament to Xinshuo’s dedication to innovation and excellence. It empowers manufacturers to achieve higher productivity, lower costs, and superior quality. Contact us at xsznjx-int.com to learn more or request a demo.