Sandwich panels are widely used in various industries due to their excellent insulation properties, durability, and lightweight structure. These panels are typically made up of two outer layers (known as the facings) and an insulating core material in between. The production of sandwich panels involves several key steps, each crucial to achieving the desired strength, thermal efficiency, and aesthetic quality. In this article, we will explore the key steps in the sandwich panel production line process in detail, from raw material preparation to the final product.
1. Raw Material Selection
The first step in the sandwich panel production line process is the selection of raw materials. The choice of raw materials plays a significant role in the performance of the sandwich panel. The primary components of a sandwich panel include the outer facings and the core material. The facings are often made from materials such as:
- Steel Sheets: Galvanized, aluminum, or coated steel sheets are commonly used for the outer layers due to their strength, corrosion resistance, and versatility.
- Insulating Core Materials: Various insulating materials are used for the core, including:
- Polyurethane (PU) Foam: Offers excellent thermal insulation and is commonly used in cold storage applications.
- Polystyrene (EPS): Provides good insulation and is cost-effective.
- Mineral Wool (Rock Wool): Offers fire resistance and is used in applications requiring higher fire safety standards.
- Polyisocyanurate (PIR): A high-performance foam material that provides superior thermal resistance.
Once the materials are selected, they are sourced from suppliers and transported to the production facility for further processing.
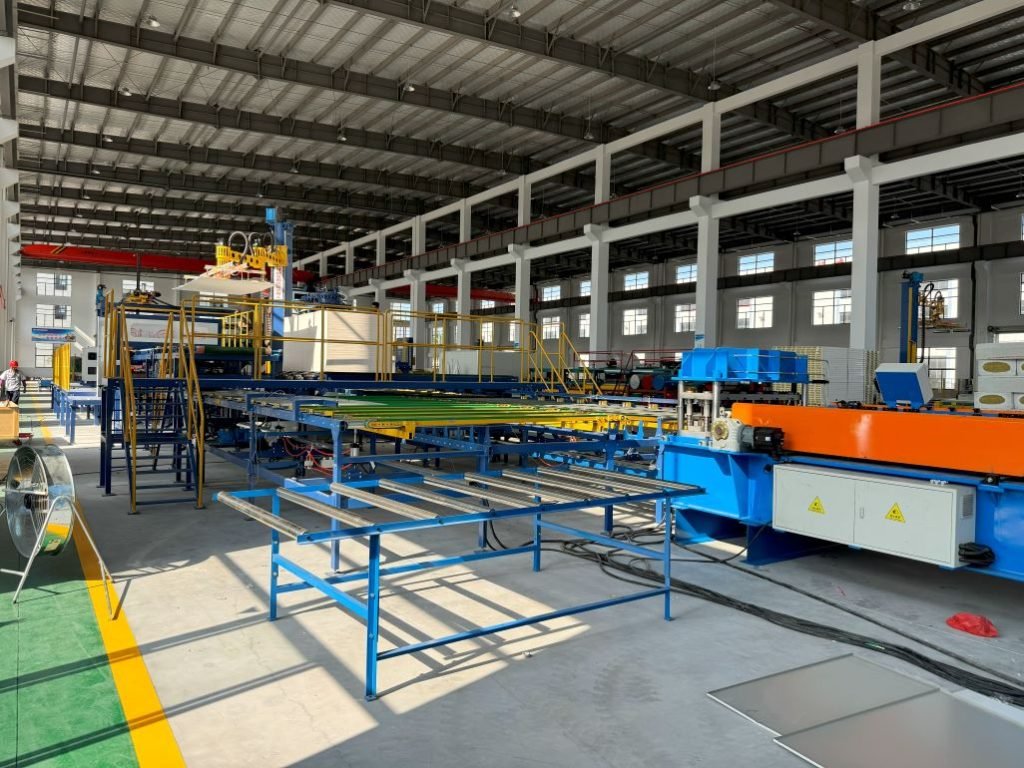
2. Cutting and Shaping
In this stage, the raw materials are cut and shaped into the desired dimensions for the sandwich panels. The steel sheets are unrolled and cut to the required width, length, and shape based on the specifications. The core material is also cut to match the size of the steel sheets.
The shaping process ensures that the core material fits perfectly between the outer facings. The core material is typically made in continuous rolls or sheets, depending on the type of insulation being used. The cutting process is highly precise, and any deviations from the specified measurements can affect the overall quality and performance of the sandwich panel.
Table 1: Common Raw Material Dimensions
Material Type | Dimensions (Width x Length) | Application |
---|---|---|
Steel Sheets | 1000mm x 2500mm (standard) | Outer facings for structural integrity |
Polyurethane Foam | 1200mm x 2500mm (standard) | Insulating core for thermal resistance |
Mineral Wool | 1200mm x 2500mm (standard) | Fire-resistant core material |
3. Core Material Preparation
Once the core material is selected and cut to size, it undergoes preparation for bonding with the facings. The preparation process typically includes pre-heating or conditioning the core material to achieve the optimal temperature and texture. This ensures better adhesion to the facings during the next steps.
In some cases, the core material is mixed with chemicals or additives to enhance its properties, such as improving fire resistance or reducing thermal conductivity. This step may vary depending on the type of core material used.
4. Bonding of Core and Facings
The next critical step is the bonding of the core material with the steel facings. This is done using a combination of heat and pressure, depending on the type of core material and adhesive used. The process is designed to ensure a strong bond between the core and facings, which is essential for the structural integrity of the sandwich panel.
For instance, in the production of PU and PIR sandwich panels, the core material is often injected between the facings, and a chemical reaction occurs, resulting in the foam expanding and bonding with the facings. For EPS panels, the core is often pre-formed and then bonded with adhesive.
The bonding process requires precise control over temperature, pressure, and timing to ensure that the final product has the required strength and insulation properties.
Table 2: Bonding Methods and Materials
Core Material | Bonding Method | Adhesive Type |
---|---|---|
Polyurethane (PU) Foam | Injection molding with chemical reaction | Polyurethane adhesive, chemical reaction |
Polystyrene (EPS) | Pre-formed core with adhesive bonding | EPS adhesive |
Mineral Wool (Rock Wool) | Laminating under heat and pressure | Resin-based adhesive, heat curing |
5. Pressing and Curing
After the core and facings are bonded together, the sandwich panel moves to the pressing and curing section. The panels are placed in a press where heat and pressure are applied to ensure that the bond between the core and facings is strong and uniform. The curing process solidifies the adhesive and ensures that the panel has the desired properties.
In the case of foam-based panels like PU or PIR, the curing process is especially critical, as it helps the foam achieve its full insulation potential. For EPS panels, the curing process helps solidify the foam, ensuring that it remains stable over time.
The pressing and curing stage also helps to remove any trapped air or excess adhesive, ensuring the panel is smooth and free of imperfections.
6. Cutting and Shaping the Finished Panels
Once the sandwich panels have been bonded and cured, they are cut to their final length and shape. This cutting process is typically done using specialized saws or cutting machines, which ensure that the edges of the panels are straight and uniform. The panels are then inspected for any defects or irregularities in size and shape.
The finished panels are typically cut into standard sizes or customized to meet specific project requirements. The panels may also undergo secondary processes, such as edge sealing, coating, or adding additional insulation layers, depending on the intended use.
7. Quality Control and Testing
Throughout the production process, quality control is essential to ensure that the sandwich panels meet industry standards and customer expectations. Quality checks are performed at every stage of the process, from raw material selection to the final inspection of finished panels.
Key quality control measures include:
- Thickness and Dimensional Accuracy: Ensuring that the panels meet the required thickness and dimensions.
- Adhesion Strength: Testing the bond between the core and facings to ensure it is strong and durable.
- Thermal Performance: Measuring the thermal conductivity of the panels to ensure they meet insulation requirements.
- Fire Resistance: For panels with fire-resistant cores, testing is done to ensure compliance with fire safety standards.
- Aesthetic Quality: Ensuring that the panels are free of cosmetic defects and have an attractive finish.
8. Packaging and Shipping
Once the panels pass the quality control tests, they are ready for packaging and shipping. The panels are carefully packed to prevent damage during transportation. Typically, the panels are stacked on pallets and wrapped to protect them from moisture, dirt, and other environmental factors. Shipping is done using trucks or containers, depending on the destination.
Table 3: Common Packaging Methods
Panel Type | Packaging Method | Packaging Material |
---|---|---|
Standard Sandwich Panels | Stacked on pallets, wrapped in plastic | Shrink-wrap, stretch film |
Customized Panels | Packed in crates, secured with straps | Wooden crates, metal bands |
Conclusion
The production of sandwich panels involves several critical steps, including raw material selection, cutting and shaping, core preparation, bonding, pressing, curing, quality control, and packaging. Each of these steps must be carefully controlled to ensure that the finished product meets the required performance standards for insulation, strength, and durability.
As a leading manufacturer and supplier of sandwich panel production lines, we offer state-of-the-art equipment designed to streamline these processes and produce high-quality sandwich panels. Our solutions are engineered to deliver excellent thermal performance, structural integrity, and aesthetic quality, making them ideal for various applications, including construction, cold storage, and more.
If you are looking to invest in a sandwich panel production line or have any inquiries regarding our products, feel free to contact us. Our team is ready to assist you with tailored solutions that meet your specific production needs.