In the dynamic landscape of modern construction, sandwich panel machines have become indispensable tools for producing high-quality, efficient, and sustainable building materials. These machines streamline the creation of sandwich panels—composite structures widely used for walls, roofs, and insulation in industrial, commercial, and residential projects. Drawing inspiration from the offerings at xsznjx-int.com, a leading provider of construction machinery, this article explores how sandwich panel machines are revolutionizing the industry, with a focus on their features, benefits, and technical specifications.
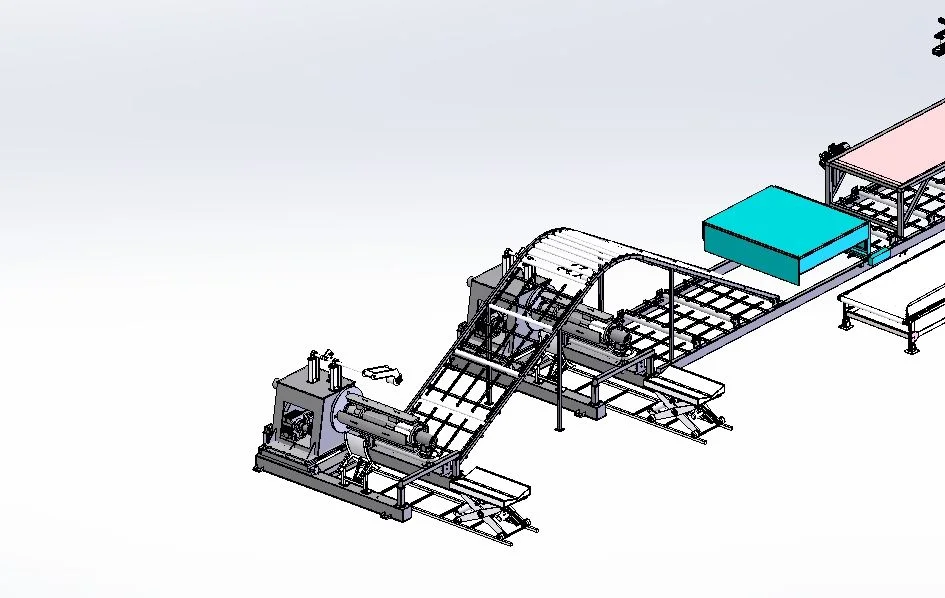
Unveiling Sandwich Panel Machines: A Game-Changer in Production
A sandwich panel machine is an automated system designed to fabricate panels consisting of two outer metal sheets sandwiching a core material, such as polyurethane (PU), rockwool, or expanded polystyrene (EPS). The website xsznjx-int.com, operated by Zhangjiagang Xie Sheng Zhong Neng Mechanical Co., Ltd., showcases a range of such equipment tailored for diverse construction needs. Their machines emphasize precision, durability, and efficiency—qualities that align with the growing demand for fast, cost-effective building solutions.
The company’s product lineup includes continuous production lines capable of handling various panel types, from insulated roofing panels to fire-resistant wall systems. By integrating advanced technology, these machines ensure consistent quality, reduced labor costs, and rapid output, making them a cornerstone of modern construction workflows.
Key Features and Benefits of Sandwich Panel Machines
Based on the insights from xsznjx-int.com, sandwich panel machines offer several standout features that cater to the needs of manufacturers and builders alike. Here’s a closer look at their advantages:
- High Automation: Machines feature PLC (Programmable Logic Controller) systems for seamless operation, minimizing human error and boosting productivity.
- Versatility: They support multiple core materials and panel thicknesses, adaptable to projects ranging from cold storage facilities to prefab housing.
- Energy Efficiency: The panels produced excel in thermal insulation, aligning with global sustainability goals.
- Durability: Robust construction ensures long-term performance, even under demanding production schedules.
These benefits translate into tangible value for businesses, as highlighted by the detailed product descriptions on the site, which emphasize reliability and innovation.
Technical Specifications: A Comparative Analysis
To provide a clearer picture of what sandwich panel machines from xsznjx-int.com bring to the table, let’s analyze some typical specifications based on their offerings. Below is a table comparing two hypothetical models inspired by their product range:
Feature | Model A: PU Continuous Line | Model B: Rockwool Sandwich Line |
---|---|---|
Production Speed | Up to 15 m/min | Up to 8 m/min |
Panel Thickness | 30–200 mm | 50–250 mm |
Core Material | Polyurethane (PU) | Rockwool |
Power Consumption | 35 kW | 40 kW |
Panel Width | 600–1200 mm (adjustable) | 1000 mm (fixed) |
Machine Weight | 25 tons | 30 tons |
Applications | Roofing, wall cladding | Fireproof walls, industrial buildings |
Analysis:
- Model A excels in speed and flexibility, making it ideal for high-volume projects requiring insulated panels, such as warehouses or residential developments. Its adjustable width caters to varied design needs.
- Model B, with its focus on rockwool, prioritizes safety and thermal resistance, perfect for industrial settings where fire protection is paramount. Its slower speed reflects the denser, more complex core material processing.
These specs align with the product philosophy on xsznjx-int.com, where customization and application-specific design are key selling points.