1. Description of the Automatic Line
Polyurethane (PUR) and Polyisocyanurate (PIR)
Polyisocyanurate, also known as PIR, is an advanced form of polyurethane (PUR). The primary advantage of PIR is its non-flammability, unlike PUR, which makes it highly successful in construction, particularly in the production of sandwich panels. Building materials based on PIR foam have been widely used in construction in Europe and the USA for a long time and have proven their effectiveness. In Russia, PIR has gained increasing popularity in recent years due to its excellent thermal insulation, durability, and fire resistance.
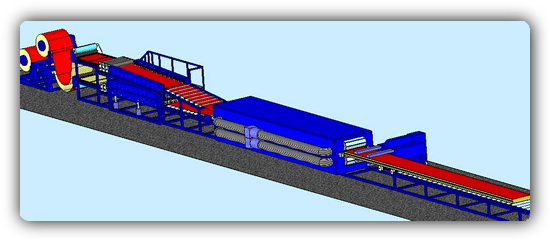
We offer an automatic production line for manufacturing sandwich panels filled with rigid polyurethane foam (PUR and PIR). Unlike traditional PUR foam panels, the new technology produces panels with fire resistance comparable to mineral wool panels. Combined with more advanced locking systems, this significantly enhances the fire resistance of the finished sandwich panels.
2. Components and Description of the Automatic Production Line
No. | Line Element Name and Brief Description | Quantity |
---|---|---|
1 | Cantilever decoiler drums, each with a lifting capacity of 10 tons. Mounted on a common structure, 3 meters long, with a 2-meter droop for the steel strip. | 2 |
2 | Upper and lower guide modules, each with an input shaft, a protective film winding unit, and a transverse cutting unit. Mounted on separate support structures. | 2 |
3 | Main forming shaft blocks, located on two levels. Each block has shafts for profile processing, supporting five profile types: smooth, linear, striped, micro-grooved, and micro-profiled. These blocks are mounted on a common support structure with the profiling modules. | 2 |
4 | Roll-forming mills, installed on two levels of the production line: – On the upper level, a reconfigurable universal mill for processing wall cladding or lower roof cladding. – On the lower level, two mills: one non-adjustable mill for profiling upper roof panels with four humps, and above it, another non-adjustable mill for profiling wall panels only. Both mills can be moved vertically using a lifting mechanism and locked in place. The mills share a common support structure with the main shaft blocks and preheating module. Each mill in the profiling module consists of 12 stands. The total length of the support structure, including the main shaft and heating zone, is 16 meters. | 3 |
5 | Steel lining preheating module, with thermal insulation, designed to preheat the steel linings after forming and before component injection (PUR or PIR). At the end of this zone, just before the hot press entrance, an injection head applies a precisely dosed mixture of components to the lower lining. | 1 |
6 | Equipment set for supplying PUR and PIR (pumps, flow meters, daily consumption tanks, etc.). | 1 |
7 | Caterpillar hot press, with upper, lower, and side caterpillar chains, adjustable in height. The number of caterpillar sets (for roof and wall panels) depends on the planned panel range. The hot press is the main module that sets the conveyor speed, with all other modules (specialized machines, decoilers) synchronized to its speed. The press speed is adjusted based on panel type and thickness with high precision. The press length ranges from 15 to 40 meters, depending on customer parameters: productivity, panel type, thickness, and other sandwich panel characteristics. Compared to PUR foam, PIR foam has a higher isocyanate-to-polyol ratio, requiring higher curing temperatures (approximately 65–70°C). Therefore, this line is equipped with a more powerful hot press. | 1 |
8 | Cross-cutting unit with a receiving roller conveyor, 20 meters long (for panels up to 12 meters). Cutting is performed with a band saw without stopping the line. Cut panels are placed on the receiving conveyor, which moves significantly faster than the main hot press conveyor, allowing quick removal of cut panels before the next panel exits the press. | 1 |
9 | Central control panel. All modules and units of the panel production line are controlled by a program from the central control panel. | 1 |
10 | Panel stabilization system. After production and cutting, panels require at least 8 hours of thermal stabilization before packaging. For a simple and cost-effective solution, several 12-meter specialized carts with sections for vertical panel placement are recommended. Panels cool gradually (thermally stabilize) in these carts before being sent to the packaging area. | 1 |
11 | Packaging module with roller conveyor. Equipped with two driven roller tables, each 12 meters long. The first roller conveyor is the feed table, where a stack of panels is formed. After forming, the stack enters the packaging area, where a rotor tightly wraps it with stretch film. The conveyor and winding machine speeds are adjustable within a wide range. | 1 |
这描述了用于连续板材生产的自动化生产线最简单、最经济的配置,仅包含必要的模块。更换钢卷需要停止生产线。要重新配置生产线以生产不同类型的夹层板、厚度或内衬颜色,也必须停止生产线。
The customer must independently provide:
- Main tanks for components (isocyanate, polyol, pentane) buried underground or placed in a separate specialized room.
- Water supply for the component thermal stabilization system near the mixing and injection head (hot water at least 60°C with a flow rate of 8–10 m³/h, and cold water not exceeding 5–7°C with a flow rate of 3–4 m³/h).
The equipment includes complete technical and operational documentation in Russian, in both paper and electronic formats.
To calculate the exact cost of the line, the following initial data are required:
- Required annual production plan.
- Required wall panel thicknesses.
- Required roof panel thickness types.
- Use of PIR and/or PUR filling.
3. Characteristics of Manufactured Sandwich Panels
Parameter | Wall Sandwich Panels | Roof Sandwich Panels |
---|---|---|
Modular Width | 1100 mm | 1075 mm |
Panel Thickness | 50 mm, 60 mm, 80 mm, 100 mm, 120 mm, 150 mm | 60 mm, 80 mm, 100 mm, 120 mm, 150 mm |
Profile Types | Smooth, linear, striped, micro-grooved, micro-profiled | Smooth, linear, striped |
4. Conveyor Speed and Line Productivity (Depending on Sandwich Panel Thickness)
Thickness of sandwich panels | Conveyor speed (m/min) | Line productivity | ||
sq.m per shift | sq.m per month | sq.m per year | ||
60mm | 6 | 2,500 | 50,000 | 600,000 |
80mm | 5 | 2 100 | 42,000 | 500,000 |
100mm | 4.3 | 1 800 | 36,000 | 430,000 |
120mm | 3.5 | 1,500 | 30 200 | 360,000 |
150mm | 3 | 1 250 | 25 200 | 300,000 |